Tribological
Tests
Since we have a wide base for testing at our disposal, we can design a testing plan, and hold the tests for various friction pairs.
The Modengy’s testing center running in Bryansk has capabilities that enable to predict operational properties of the friction units early on the designing stage.
We help the industrial enterprises estimate such important parameters as friction coefficient, wear intensity, frictional heating.
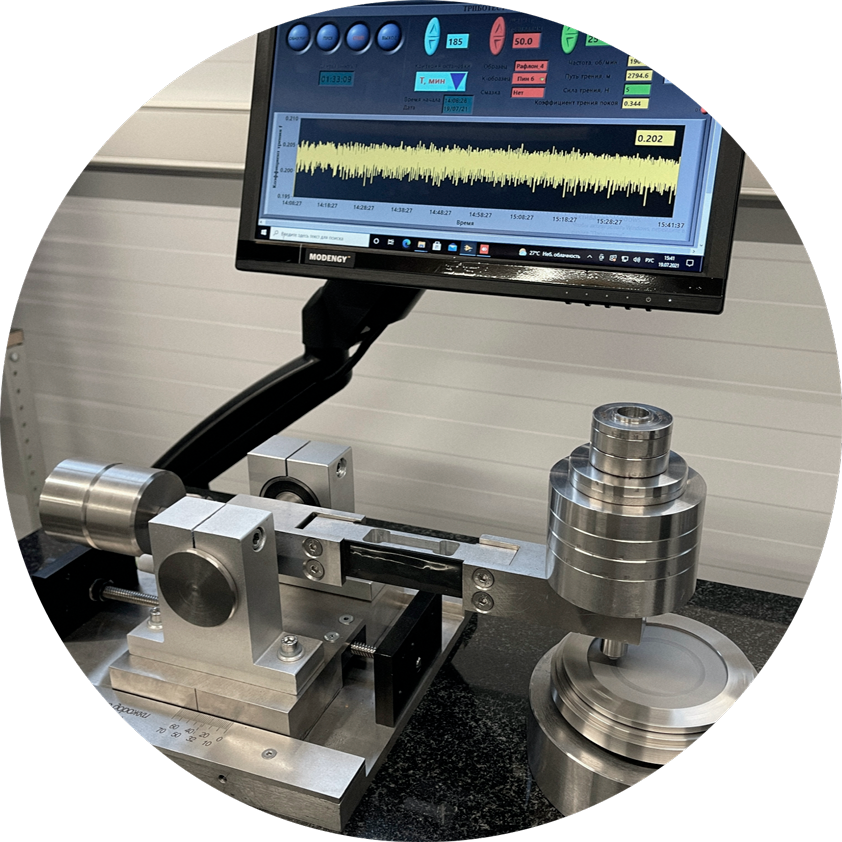
What does this service include?
- Data collecting to make up the technical specification
- Analysis of the currently used solutions and testing techniques
- Design documentation and experiment outline development
- Experiment holding
- Analysis of the results, and drawing up of accounts
- Detailed report, and engineering and design recommendations on optimizing the friction unit that are provided to the customer
- All the rights for the test results pointed in the report are transferred to the customer
Types of the tests
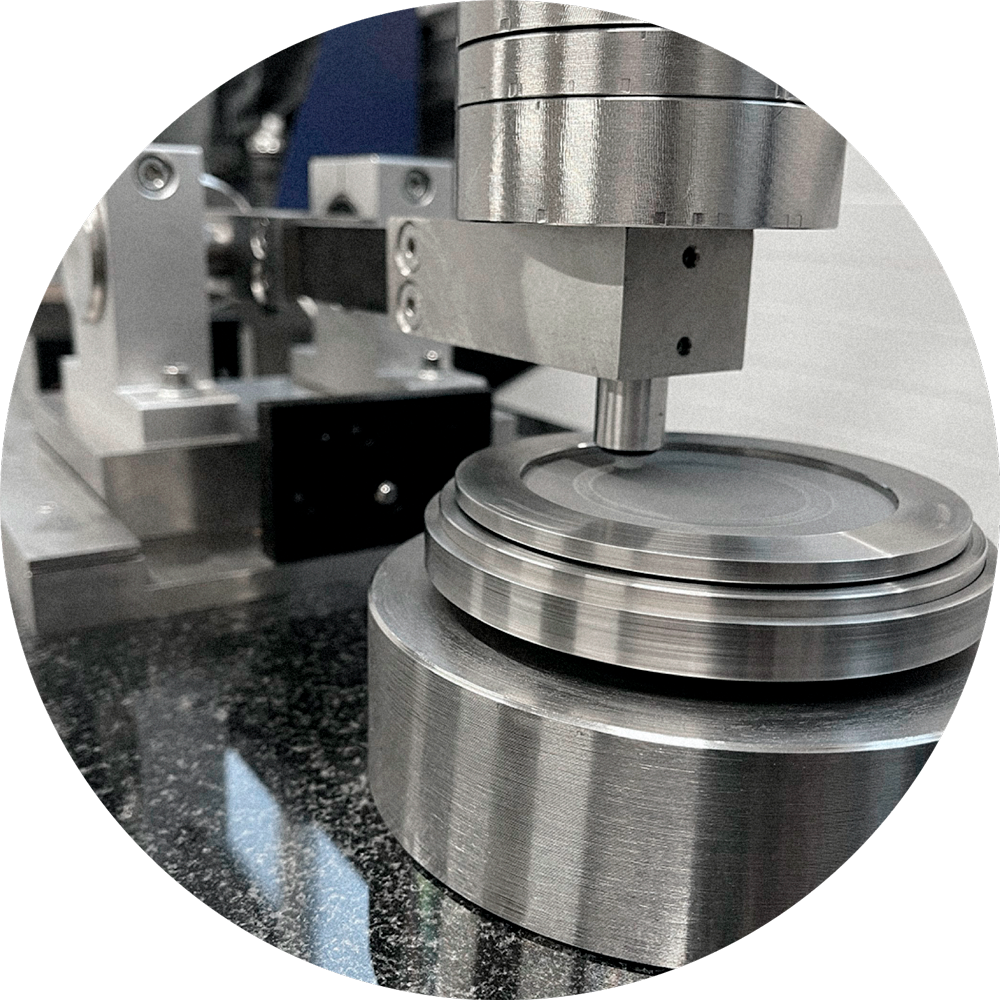
- Matching the optimal friction pair for the given operational conditions
- Measuring friction coefficient in the friction pair, and its change dynamics
- Detecting wear resistance of the friction pair
- Detecting friction and wear features of the coatings
- Revealing various factors impact onto the characteristics of the tribological conjunctions (contact pressure, slide rate, operational medium type)
- Detecting anti-friction and wear-resistant properties of the lubricating materials
- Measuring frictional heating temperature
- Modeling the friction unit operating
- Researching the running-in ability characteristics
The tests according to the Reichert method
Such scheme of testing is intended to assess anti-wear and anti-scuffing properties of the constructive and lubricating materials. This test is especially topical in the fields of industry where lubricating materials are used under conditions of increased loads.
The tests according to the Reichert method are used for both quality control, and to research new lubricating materials.
According to the results of these tests value of linear wear on the fixed roller is detected, and value of linear wear intensity of the counterbody is calculated as the ratio of the linear wear to the friction path.
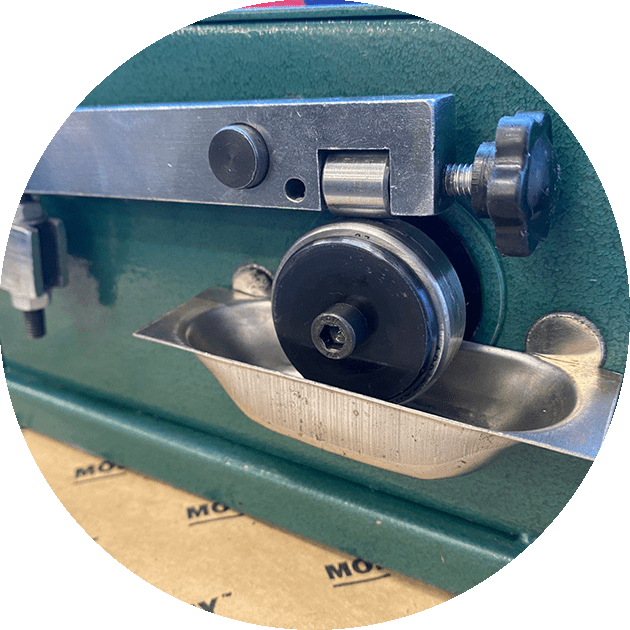
Due to use of the system approach, it gets possible to achieve the required output parameters such as friction coefficient, and wear intensity by changing the certain system elements in a desirable direction.
Now, the partners can watch fulfilling their orders in the real time mode. More than that, there is an opportunity to observe both the process itself, and its results which are displayed on the friction machine screen.
If you are interested in holding tribotechnical tests, apply to the Modengy company, please.